By following these points when preparing the cutting fluid, you can eliminate or control machine tool corrosion!
Dec 02,2024
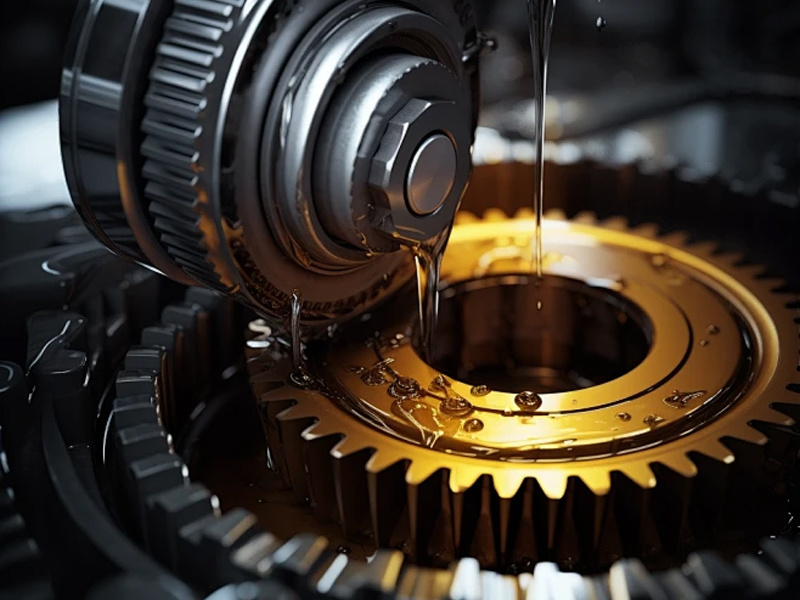
The state of cutting fluid in equipment usage lacks effective detection and maintenance methods, leading to machine tool failures after a period of use. It was found that the electrical lines and built-in systems of the machine tool experienced severe corrosion caused by cutting fluid, resulting in hidden faults in the equipment's electrical system. The downtime due to these faults has severely affected normal production. Therefore, while using cutting fluid, we should take the following specific control measures for rectification.
1. Increase process requirements; before production processing of the workpiece blank, add a shot peening process to eliminate impurities such as rust and sand particles.
2. Do not use lime water in the marking process to eliminate corrosion caused by lime deposits on the equipment.
3. Through comparative tests of several water-based cutting fluids, select a cutting fluid with higher comprehensive performance and better rust prevention properties.
4. Use purified water instead of tap water to prepare cutting fluid. Although the cost increases, it can improve the comprehensive performance indicators of water-based cutting fluid, extend its service life, and provide better rust prevention for the equipment.
5. Establish a regular inspection system for cutting fluid and keep records. Require operators to regularly test the cutting fluid concentration, pH value, and other indicators. If the cutting fluid deteriorates, it should be replaced in a timely manner, and new fluid should be added according to concentration changes to ensure the quality of the cutting fluid.
6. Require cutting fluid manufacturers to regularly test indicators such as bacterial content and chloride ion content, and assist and guide operators in monitoring cutting fluid indicators.
7. Daily inspection of the cutting fluid filtration device status of the equipment is necessary to ensure its normal operation; the cooling system should be cleaned at least twice a year using a system cleaning agent.
8. Regularly inspect the sealing performance of the equipment, and promptly repair any issues found to prevent cutting fluid from entering the machine tool.
9. Regularly clean areas prone to residual cutting fluid, such as the tool library and workbench, with cutting fluid to avoid corrosion.
Through the summary analysis of the above case of cutting fluid corrosion on machine tools, it is concluded that the factory workshop did not pay attention to the use and management of cutting fluid, resulting in equipment failure and affecting normal production. After the corrosion problem of the machine tool appeared, the factory workshop should have promptly taken effective control measures after jointly diagnosing and analyzing with the manufacturer.
Next:
Contact Us
E-mail:
Weihao@barens.cn
Mobile/Wechat/Whatsapp:
+(86)18595692582
Address:
No.9, Industrial Zone, Wangqu Village, Qinyang City, Jiaozuo City, Henan Province, China
TEL: +86 037186158618
Fax number: +86371-86158608
Contacts: Davi
Mobile/Wechat/Whatsapp: (+86)18595692582
Email: weihao@barens.cn
Contacts: Doris
Mobile/Wechat/Whatsapp: (+86)18211801290
E-mail: Doris@barens.cn
Address:No.9, Industrial Zone, Wangqu Village, Qinyang City, Jiaozuo City, Henan Province, China
Website construction: 300.cn | SEO | Digital card
This site supports IPV4/IPV6 access
COOKIES
Our website uses cookies and similar technologies to personalize the advertising shown to you and to help you get the best experience on our website. For more information, see our Privacy & Cookie Policy
COOKIES
Our website uses cookies and similar technologies to personalize the advertising shown to you and to help you get the best experience on our website. For more information, see our Privacy & Cookie Policy
These cookies are necessary for basic functions such as payment. Standard cookies cannot be turned off and do not store any of your information.
These cookies collect information, such as how many people are using our site or which pages are popular, to help us improve the customer experience. Turning these cookies off will mean we can't collect information to improve your experience.
These cookies enable the website to provide enhanced functionality and personalization. They may be set by us or by third-party providers whose services we have added to our pages. If you do not allow these cookies, some or all of these services may not function properly.
These cookies help us understand what you are interested in so that we can show you relevant advertising on other websites. Turning these cookies off will mean we are unable to show you any personalized advertising.
SAF Coolest v1.3.1.2 设置面板 GAGSD-AGYF-JAAAE-ADE
无数据提示
Sorry, the current column is being updated, please look forward to it!
You can view other columns or returnHome Page