Choosing the Right Industrial Cutting Fluid for Your Machinery: A Comprehensive Guide
Jul 15,2025
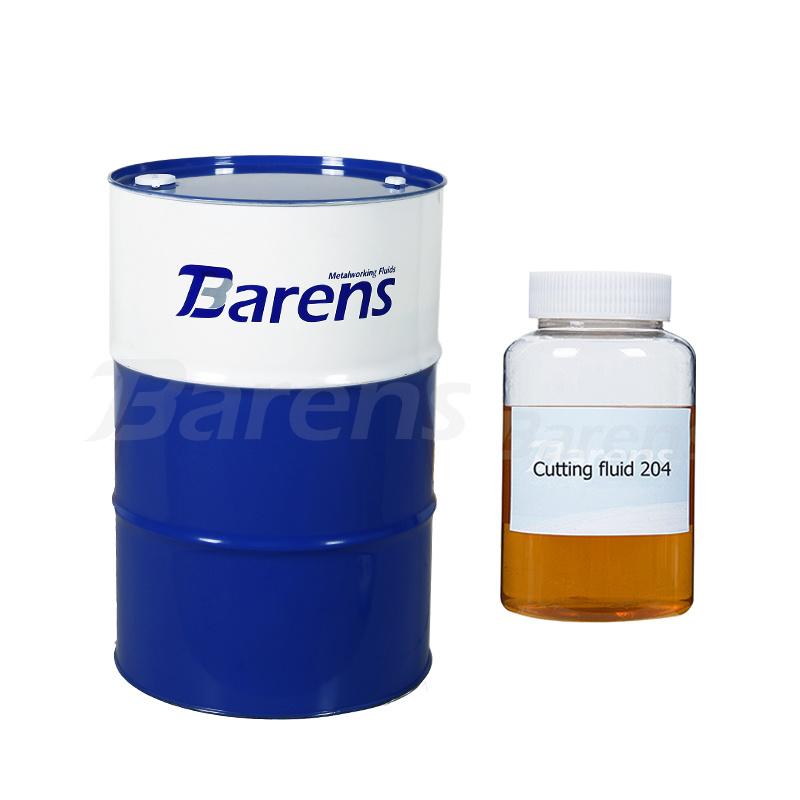
Choosing the Right Industrial Cutting Fluid for Your Machinery
Table of Contents
- Introduction to Industrial Cutting Fluids
- Types of Industrial Cutting Fluids
- Factors to Consider When Choosing Cutting Fluids
- Application Techniques for Cutting Fluids
- Maintenance and Monitoring of Cutting Fluids
- Common Mistakes to Avoid
- FAQs About Industrial Cutting Fluids
- Conclusion
Introduction to Industrial Cutting Fluids
When it comes to enhancing the efficiency of your machining operations, **choosing the right industrial cutting fluid** is absolutely crucial. These fluids play a pivotal role in reducing friction and heat, which in turn helps to maintain tool life, improve surface finish, and enhance overall productivity. As industries evolve, the demand for high-performance fluids tailored to specific applications continues to grow. This article aims to provide a comprehensive overview of **industrial cutting fluids**, guiding you through the selection process to ensure you make informed decisions for your machinery.
Types of Industrial Cutting Fluids
Understanding the different types of cutting fluids available is essential for making an informed choice. Each category has its own unique properties and benefits.
Water-Soluble Fluids
Water-soluble cutting fluids are popular due to their versatility and cooling capabilities. Composed of oil emulsions mixed with water, they provide excellent lubrication and cooling during machining processes. Their ability to carry away heat effectively makes them suitable for various machining operations. However, they require proper maintenance to prevent bacterial growth and ensure optimal performance.
Straight Oils
Straight oils, also known as non-emulsifiable oils, consist of mineral oil and additives. They are particularly effective for operations that require high lubrication, such as grinding and machining tough materials. One of the main advantages of straight oils is that they offer superior lubricating properties, which enhances tool life. However, they lack the cooling properties of water-soluble fluids, making them less suitable for high-speed operations.
Synthetic Fluids
Synthetic cutting fluids are formulated from chemical compounds rather than petroleum products. These fluids provide excellent lubrication and cooling, making them an ideal choice for various high-speed machining processes. They often contain fewer contaminants and are less likely to cause corrosion, which aids in prolonging the life of your machinery. Additionally, synthetic fluids are more environmentally friendly, as they have a reduced impact on health and safety compared to traditional oils.
Factors to Consider When Choosing Cutting Fluids
Selecting the appropriate cutting fluid involves evaluating several key factors to ensure it aligns with your specific machining requirements.
Material Compatibility
Assessing the compatibility of the cutting fluid with the materials being machined is essential. Different metals and alloys may react differently to various cutting fluids. For instance, aluminum-based materials often require fluids that prevent corrosion and oxidation. Furthermore, ensuring compatibility minimizes the risk of contamination and prolongs the life of the cutting tools.
Machining Process
The type of machining process you employ significantly influences your choice of cutting fluid. Whether you are engaged in turning, milling, drilling, or grinding, each operation may require a specialized fluid to maximize performance. For example, high-speed machining often benefits from fluids that provide exceptional cooling properties, while heavy-duty operations may require fluids with superior lubrication.
Cooling Properties
Effective cooling is vital for preventing overheating during machining operations. The cutting fluid should efficiently dissipate heat away from the cutting zone, thereby maintaining optimal temperatures that prevent tool wear and improve surface finish. Evaluate the thermal conductivity and heat transfer capabilities of cutting fluids to ensure they meet your operational needs.
Environmental Impact
In today's eco-conscious world, selecting cutting fluids with minimal environmental impact is paramount. Synthetics and biodegradable options are increasingly popular, as they reduce harmful emissions and waste. Opting for environmentally friendly fluids not only adheres to regulatory standards but also enhances your company's sustainability initiatives.
Application Techniques for Cutting Fluids
The application method of cutting fluids can significantly affect their performance. Proper application techniques ensure effective cooling and lubrication, enhancing machining efficiency.
Flood Cooling
Flood cooling involves applying a continuous stream of cutting fluid to the cutting area, effectively cooling the tool and workpiece. This method is particularly useful for high-speed machining operations, where heat generation is significant.
Mist Cooling
Mist cooling disperses cutting fluid in aerosol form, allowing for better coverage of the cutting area. This technique is beneficial for smaller machining setups, as it reduces fluid consumption while maintaining adequate lubrication.
Manual Application
For operations requiring precise control, manual application of cutting fluids may be employed. This method allows for targeted application, reducing waste and ensuring that the fluid is applied only where it is needed.
Maintenance and Monitoring of Cutting Fluids
Regular maintenance and monitoring are essential to ensure the longevity and effectiveness of cutting fluids. Establish a routine for checking fluid levels, concentrations, and contamination levels.
Fluid Maintenance
Conduct periodic analysis to determine the fluid's performance characteristics. This may involve testing for pH levels, bacterial growth, and the presence of contaminants. Regular maintenance helps prevent issues such as foaming, rancidity, and tool corrosion.
Fluid Replacement
Replacing cutting fluids at appropriate intervals is crucial for maintaining optimal machining performance. Signs that indicate a need for replacement may include a significant drop in cooling efficiency, unpleasant odors, or visible contamination.
Common Mistakes to Avoid
Navigating the world of cutting fluids can be challenging, and several common mistakes can hinder performance.
Choosing Based on Price Alone
While cost is a factor, selecting cutting fluids based solely on price can lead to subpar performance. Consider the long-term benefits associated with higher-quality fluids.
Neglecting Fluid Compatibility
Failing to assess compatibility with materials can lead to significant issues, including increased wear on tools and poor finished product quality. Always verify compatibility before making a selection.
Ignoring Environmental Considerations
Overlooking the environmental impact of cutting fluids can result in regulatory issues and damage to your company's reputation. Prioritize eco-friendly options to align with contemporary industry standards.
FAQs About Industrial Cutting Fluids
What are the primary functions of industrial cutting fluids?
Industrial cutting fluids serve multiple functions, including cooling the cutting zone, reducing friction, lubricating tools, and helping to remove chips from the work area. They play a critical role in extending tool life and improving surface finish.
How often should I change my cutting fluid?
The frequency of changing cutting fluid depends on its type, usage levels, and contamination levels. Regular monitoring and analysis will help determine the optimal replacement intervals.
Can I mix different types of cutting fluids?
Mixing different types of cutting fluids is generally not recommended, as it can lead to adverse reactions, reduced performance, and increased risk of contamination. Always consult with the manufacturers for guidance.
What are the signs that my cutting fluid is contaminated?
Signs of contamination include foul odors, discoloration, excessive foam, and visible debris in the fluid. Regular monitoring can help identify contamination early.
Are synthetic cutting fluids superior to mineral oils?
Synthetic cutting fluids often provide better cooling and lubrication properties compared to mineral oils. Additionally, they are less likely to support bacterial growth and have a reduced environmental impact. However, the best choice ultimately depends on specific machining needs.
Conclusion
Selecting the right industrial cutting fluid for your machinery is a critical decision that can significantly impact your operational efficiency and product quality. By understanding the various types of cutting fluids, considering key factors such as material compatibility and cooling properties, and employing effective application techniques, you can ensure optimal performance in your machining processes. Remember to maintain and monitor your cutting fluids regularly to maximize their benefits and avoid common pitfalls. With the right approach, your machinery will perform at its best, leading to enhanced productivity and a competitive edge in the industrial landscape.
Previous:
Contact Us
E-mail:
Weihao@barens.cn
Mobile/Wechat/Whatsapp:
+(86)18595692582
Address:
No.9, Industrial Zone, Wangqu Village, Qinyang City, Jiaozuo City, Henan Province, China
TEL: +86 037186158618
Fax number: +86371-86158608
Contacts: Davi
Mobile/Wechat/Whatsapp: (+86)18595692582
Email: weihao@barens.cn
Contacts: Doris
Mobile/Wechat/Whatsapp: (+86)18211801290
E-mail: Doris@barens.cn
Address:No.9, Industrial Zone, Wangqu Village, Qinyang City, Jiaozuo City, Henan Province, China
Website construction: 300.cn | SEO | Digital card
This site supports IPV4/IPV6 access
COOKIES
Our website uses cookies and similar technologies to personalize the advertising shown to you and to help you get the best experience on our website. For more information, see our Privacy & Cookie Policy
COOKIES
Our website uses cookies and similar technologies to personalize the advertising shown to you and to help you get the best experience on our website. For more information, see our Privacy & Cookie Policy
These cookies are necessary for basic functions such as payment. Standard cookies cannot be turned off and do not store any of your information.
These cookies collect information, such as how many people are using our site or which pages are popular, to help us improve the customer experience. Turning these cookies off will mean we can't collect information to improve your experience.
These cookies enable the website to provide enhanced functionality and personalization. They may be set by us or by third-party providers whose services we have added to our pages. If you do not allow these cookies, some or all of these services may not function properly.
These cookies help us understand what you are interested in so that we can show you relevant advertising on other websites. Turning these cookies off will mean we are unable to show you any personalized advertising.
SAF Coolest v1.3.1.2 设置面板 GAGSD-AGYF-JAAAE-ADE
无数据提示
Sorry, the current column is being updated, please look forward to it!
You can view other columns or returnHome Page