The Science Behind Effective Coolants for Aluminium Machining: Maximizing Efficiency and Precision
Jul 01,2025
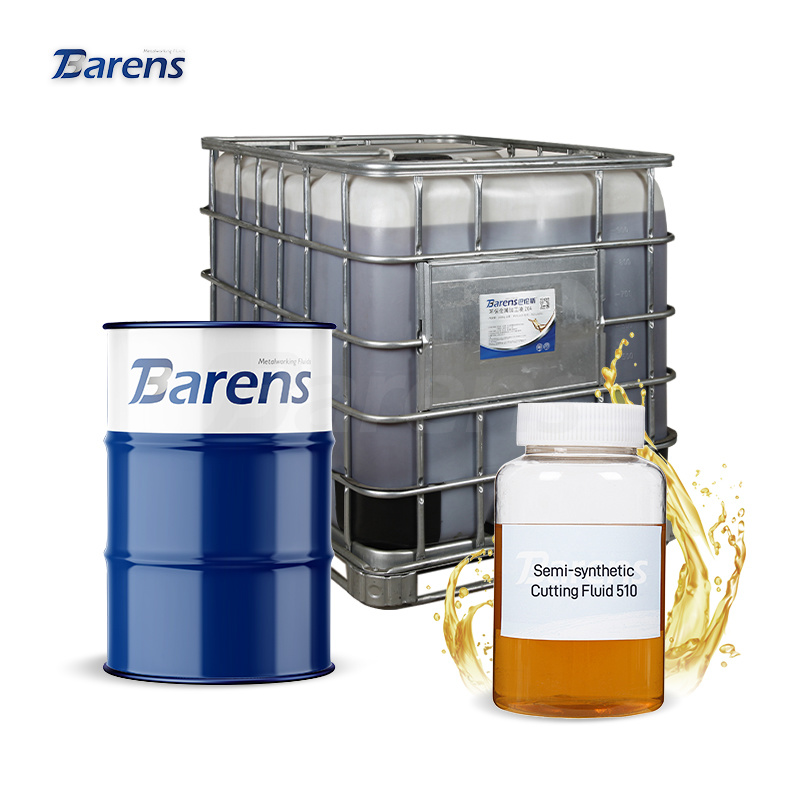
The Science Behind Effective Coolants for Aluminium Machining
Table of Contents
- 1. Introduction to Aluminium Machining
- 2. The Importance of Coolants in Aluminium Machining
- 3. Types of Coolants for Aluminium Machining
- 4. Properties of Effective Coolants
- 5. Impact of Coolants on Productivity
- 6. Environmental Considerations in Coolant Usage
- 7. Frequently Asked Questions
- 8. Conclusion
1. Introduction to Aluminium Machining
Aluminium machining is a critical process in the manufacturing sector, characterized by the manipulation of aluminum materials to create precision components. Given its lightweight and malleable nature, aluminum is extensively used in various applications, including aerospace, automotive, and consumer electronics. Despite its advantages, machining aluminum poses unique challenges, particularly regarding heat generation and tool wear.
2. The Importance of Coolants in Aluminium Machining
Effective cooling mechanisms play a crucial role in improving machining efficiency. Coolants serve several purposes, including:
- **Heat Removal**: Machining processes generate significant heat, which can lead to thermal distortion of the workpiece and premature tool wear. Coolants help dissipate this heat effectively.
- **Lubrication**: They reduce friction between the tool and the workpiece, leading to smoother operations and longer tool life.
- **Chip Removal**: Coolants facilitate the removal of chips and debris from the machining area, preventing interference with the machining process and ensuring a cleaner work environment.
Understanding the science behind coolants is essential for optimizing these benefits in aluminum machining.
3. Types of Coolants for Aluminium Machining
Various coolant types are available, each with its specific properties and applications. Choosing the right coolant is vital for achieving optimal performance in aluminum machining.
3.1 Water-Soluble Coolants
Water-soluble coolants are popular due to their excellent cooling properties and cost-effectiveness. These coolants, which typically consist of a mixture of water and additives, offer:
- **High Heat Dissipation**: The water component provides superior thermal conductivity.
- **Biostability**: Many modern formulations are designed to resist bacterial growth, enhancing their longevity.
- **Versatility**: Water-soluble coolants are suitable for various machining operations, including milling, turning, and grinding.
However, they may require additional care to prevent rust and corrosion on machining equipment.
3.2 Oil-Based Coolants
Oil-based coolants are formulated primarily from petroleum oils and are known for their excellent lubricating properties. Their benefits include:
- **Effective Lubrication**: They significantly reduce friction, which can enhance tool life and surface finish.
- **Heat Resistance**: Oil-based coolants can withstand higher temperatures without breaking down.
- **Reduced Mist Formation**: They produce less mist than water-soluble options, contributing to a safer working environment.
However, these coolants may not provide as much heat transfer efficiency as water-based solutions.
3.3 Synthetic Coolants
Synthetic coolants do not contain oil and are formulated from chemical compounds designed to provide both cooling and lubricating effects. Their advantages include:
- **Low Viscosity**: This property allows for better chip removal and reduced buildup.
- **Environmental Friendliness**: Many synthetic coolants are biodegradable and less harmful to the environment.
- **Stable Performance**: They maintain their properties over various temperature ranges and machining conditions.
Synthetic coolants are often the choice for high-performance applications, though they can be more expensive than traditional options.
4. Properties of Effective Coolants
To achieve optimal performance in aluminum machining, coolants must possess specific properties that enhance their effectiveness.
4.1 Thermal Conductivity
Thermal conductivity is a critical factor in a coolant's ability to transfer heat away from the machining zone. Higher thermal conductivity ensures efficient heat removal, reducing the risk of thermal damage to both the tool and the workpiece. Therefore, selecting a coolant with optimal thermal properties is essential for maintaining performance.
4.2 Lubricating Properties
Effective lubrication minimizes friction and wear on the cutting tools. Coolants with superior lubricating properties contribute to improved surface finishes and extended tool life. The selection of coolants that offer both cooling and lubrication is vital for achieving optimal machining results.
4.3 Corrosion Inhibition
Corrosion of machinery and components can be a significant issue in machining. An effective coolant should contain corrosion inhibitors that protect both the workpiece and the equipment from rust and degradation, ensuring the longevity of tools and machinery.
5. Impact of Coolants on Productivity
The choice of coolant can significantly influence overall productivity in aluminum machining operations. Effective coolants can lead to:
- **Faster Machining Speeds**: By reducing heat and friction, operators can increase feed rates and cutting speeds.
- **Improved Tool Life**: Enhanced lubrication and cooling properties can extend the life of cutting tools, reducing downtime for replacements.
- **Higher Product Quality**: Proper cooling and lubrication lead to fewer defects, better surface finishes, and more precise dimensions, contributing to higher customer satisfaction.
Investing in the right coolant can yield substantial returns in productivity and efficiency.
6. Environmental Considerations in Coolant Usage
As industries increasingly focus on sustainability, the environmental impact of coolants is an important consideration. Choosing biodegradable and non-toxic coolants can help mitigate environmental harm. Additionally, proper disposal and recycling of used coolants play crucial roles in reducing the ecological footprint of machining operations.
7. Frequently Asked Questions
1. What are the main functions of coolants in aluminum machining?
Coolants serve to remove heat, reduce friction, and facilitate chip removal during machining. They also help maintain tool life and improve workpiece quality.
2. How do I choose the right coolant for my machining operation?
Consider factors such as the type of machining process, the specific properties of the coolant (e.g., thermal conductivity, lubrication), and environmental regulations when selecting a coolant.
3. Are synthetic coolants better than oil-based coolants?
Synthetic coolants offer advantages in terms of biodegradability and stable performance, but the choice depends on specific machining applications and requirements.
4. How often should I replace my coolant?
The frequency of coolant replacement depends on usage, contamination levels, and the specific properties of the coolant. Regular monitoring can help determine the best schedule for replacement.
5. Can I mix different types of coolants?
Mixing different coolant types is generally not recommended, as it can lead to reduced performance and potential chemical reactions. Always consult manufacturer guidelines before mixing.
8. Conclusion
The science behind effective coolants for aluminum machining is fundamental to optimizing manufacturing processes. By understanding the different types of coolants, their properties, and their impact on productivity, manufacturers can make informed choices that enhance efficiency and precision in machining operations. In a competitive environment, investing in the right coolant not only extends tool life and improves surface finishes but also contributes to a more sustainable manufacturing practice. As technology advances, staying updated on the latest coolant innovations will be key to maintaining a competitive edge in aluminum machining.
Previous:
Contact Us
E-mail:
Weihao@barens.cn
Mobile/Wechat/Whatsapp:
+(86)18595692582
Address:
No.9, Industrial Zone, Wangqu Village, Qinyang City, Jiaozuo City, Henan Province, China
TEL: +86 037186158618
Fax number: +86371-86158608
Contacts: Davi
Mobile/Wechat/Whatsapp: (+86)18595692582
Email: weihao@barens.cn
Contacts: Doris
Mobile/Wechat/Whatsapp: (+86)18211801290
E-mail: Doris@barens.cn
Address:No.9, Industrial Zone, Wangqu Village, Qinyang City, Jiaozuo City, Henan Province, China
Website construction: 300.cn | SEO | Digital card
This site supports IPV4/IPV6 access
COOKIES
Our website uses cookies and similar technologies to personalize the advertising shown to you and to help you get the best experience on our website. For more information, see our Privacy & Cookie Policy
COOKIES
Our website uses cookies and similar technologies to personalize the advertising shown to you and to help you get the best experience on our website. For more information, see our Privacy & Cookie Policy
These cookies are necessary for basic functions such as payment. Standard cookies cannot be turned off and do not store any of your information.
These cookies collect information, such as how many people are using our site or which pages are popular, to help us improve the customer experience. Turning these cookies off will mean we can't collect information to improve your experience.
These cookies enable the website to provide enhanced functionality and personalization. They may be set by us or by third-party providers whose services we have added to our pages. If you do not allow these cookies, some or all of these services may not function properly.
These cookies help us understand what you are interested in so that we can show you relevant advertising on other websites. Turning these cookies off will mean we are unable to show you any personalized advertising.
SAF Coolest v1.3.1.2 设置面板 GAGSD-AGYF-JAAAE-ADE
无数据提示
Sorry, the current column is being updated, please look forward to it!
You can view other columns or returnHome Page